Valves for PVC Service
PVC (Polyvinyl Chloride) is the third largest-selling plastic in the world after polyethylene and polypropylene. Over half of the world’s PVC is made using our valves. PVC's low cost, excellent durability and ease of molding make it the material of choice for dozens of industries from construction (rigid grades for PVC pipe and windows) to coatings (electrical) and flexible extruded part (hoses and footwear).
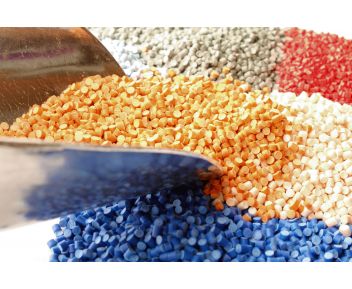
PVC Process
There are many PVC processes including SPVC, EPVC, CPVC and bulk PVC. Suspension (80% of the world capacity) and Emulsion PVC with finer particle size are the most common processes. However many of the issues are the same. The polymerization - done in a suspension reactor – has special issues. The reactor is filled with VCM (monomer) and water. The highly toxic nature of the VCM monomer gives problems throughout the process.
Valve Requirements
Valves therefore need to be leak free and and ensure zero emissions to atmosphere. The Fetterolf Ram-Seal Spray Rinse Valve meets all of these conditions and more. Similarly the best reactor drain valve such as the Rod-Seal Valve is one that does not offer any dead space for media remnants to react and solidify in the valve.
Typical sizes of reactors are from 80 to 120m3, with some as large as 200m3. A high speed mixer keeps the batch in continuous suspension. Initiators are added each with a variety of characteristics. Once the reaction has finished, the PVC slurry is drained and degassed. Great care is required to ensure removal of effectively all the VCM (less than 1 ppm residual). The polymer is dried and shipped.
Closed Reactor Technology
Fetterolf spray rinse valves were key to the development of closed reactor technology – a breakthrough in both cost reduction and product quality. The residual PVC must be removed after every batch to ensure product quality and effective temperature control of the reaction. This technology allows the reactor to be automatically rinsed after every batch without ever exposing the reactor ID to the atmosphere.
Enhanced Reactor Cleaning
Our development of the spray rinse valve made this process practical. As each reactor is different, the rinse pattern for the spray rinse valves varies. The larger the reactor, the more complex the rinsing job. For 200m3 reactors, four spray rinse valves are carefully located onto the reactor head. For smaller – for example 100m3 – two are required. Water rinse pressures are between 10 and 30 bar. Above and below these pressures, rinse performance is reduced. This technology resulted in a huge increase in productivity as well as higher quality product and is now the standard of the industry.
Enhanced Draining
While the closed reactor technology made a leap forward in efficiency – more PVC batches of higher quality per
day – there are all sorts of smaller gains thru new valve designs. For example the high speed drain valve with fast acting actuator – AC or special electric – as well as large port size, can drain the reactor more quickly and reduce the rinse cycle. The seatless valve concept of the Rod-Seal Valve means that there are no dead spaces for medium to react or solidify in the valve, thus ensuring continued operation and low maintenance.
As opening a reactor with a toxic material like VCM takes time and money, the Fetterolf design have moved most of the repair tasks to the exterior of the valve. For example seal and packing can be re-tightened again and again to compensate for wear. All without opening the reactor. All of these factors save time and time can be equated to more batches and greater profit.
Steam Injection and kill valves
To complement the critical drain and spray rinse valves, Fetterolf also provides are range of designs for steam and kill process injection valves. These valves can be Ram valves (Ram-Seal) or special design short stroke disc valves. Whatever you requirement, Fetterolf has the exact fit for your PVC process or plant conditions.